In recent years, "CTP" technology has become a hot topic in major print media. Domestically powerful companies have also introduced CTP plate making equipment to establish a corporate image and improve their competitiveness. However, having the most expensive and most advanced equipment is just a good reputation. For companies that own CTP plate making equipment, the most practical thing is to reduce costs and create maximum profits.
The company's Xi'an Coal Airline Map Printing and Printing Company introduced the Heidelberg CTP plate making equipment in October 2001. From equipment installation and commissioning to scale production, the author had the honor of having been on the battle line, deeply impressed by the fact that Production cost is an effective way to use CTP equipment to maximize profits.
For an independent accounting platemaking shop, the cost of a CTP plate-making process is much higher than that of the film-making process, if only from the perspective of material use. The process of our company's film making process is: film output→printing and printing→dyeing and proofing; the CTP plate making process is: digital proofing→patching→changing→CTP output. With CTP version 100 yuan / Zhang, film 53 yuan / m 2, renewable PS version of 20 yuan / pair open, high light photo paper is 6 yuan / m 2 calculation, with a set of large four-color live (87cm x 57cm) For example, the cumulative cost of consumables for the film process is: 0.87 x 0.57 x 4 x 53 (film) + 4 x 20 (plate) = 185.13 yuan; and the cost of the CTP process is: 0.87 x 0.57 x 6 (digital proof) + 100 ×4 (plate material) = 402.98 yuan.
From the above data, it can be seen that the cost of the CTP plate making process is more than 2 times higher than that of the film plate making process. The main reason for this result is the high price of the CTP plate material. At the present stage, the CTP plate used by our company (Kodak Bolilite's plate) still relies on imports. Although we can not reduce the cost in terms of price, we can minimize the waste disposal rate in each production and fully reflect the CTP plate making. The advantage of the network is to attract customers with advantages such as high copying precision, rich image layers, and shorter operating time, which creates profits for the entire company (in fact, if the cost of the integrated printing shop plate, the CTP plate making process and the film making process The cost is almost equivalent).
In the past year, the author has accumulated some methods to reduce the scrapping rate and make up the version. I would like to share it with my colleagues.
1. Keep the PS version clean and smooth
The Topsetter 102 is an external drum type plate making machine, which requires a particularly high degree of cleanliness and flatness of the plate material, especially when it comes to the work of the frequency modulation network. In the initial period of CTP use, the gradation hopping phenomenon often occurs on the flat screen when working out the frequency adjustment network. (A small area with a deeper level is visible to the naked eye. Observable under the magnifying glass is that the network is significantly denser than the surrounding area.) . Excluding the cause of the document itself, after repeated experiments and analysis, it was finally found that dust or irregularities on the plate resulted in uneven heat absorption during exposure, resulting in uneven thermal cross-linking reactions.
For these reasons, we require that the operator must wear clean work gloves when loading CTP plates, and then pull the vertical printing materials from the plate directly into the entrance of the Topsetter 102, and must avoid folding during the transport process. Edition (My company uses Kodak PolyLight's Graphics 0770 × 1030 plate, thickness of only 0.3mm, very easy to fold version).
2. Addition and deletion of content on the plate
Although the customer's sample proofs for digital proofing have been signed and used by the CTP system before outputting the plates, and the quality inspectors have also conducted strict proofreading, there are still problems with the contents of the individual printed materials inevitably after the plates have been printed. For example, sometimes there is a lack of one or two field content (such as lines, punctuation marks, etc.) with a dot percentage of 100%. If there is no color fit, the plate will not need to be re-used. The following method can be used to make up: First wipe off the protective glue on the printing plate, mark it on the printing plate with a squeegee (use a moderate force), and then put on the ink, and then wipe on the protective glue (but this edition cannot exceed 3,000 prints).
If there is any extra content on the plate, if it does not involve color fitting, it can be repaired with Xingguang PS plate version, wiped clean with water, and then wipe with peach gum.
3. Dirty processing of printing plates in the publishing process
The plate used by Topsetter 102 is a thermal CTP plate. When the temperature exceeds a critical value during exposure, a cross-linking reaction occurs in the image and forms a latent image. During development, this portion is insoluble in the developer while the unexposed blank portion is The resin layer was dissolved in the developer because no cross-linking reaction occurred. After a certain period of time after a certain amount of plate material has been developed, a portion of the resin layer in the developer solution will form a lot of floc and adhere to the finished plate material. If it is not treated, it will cause the printing to be dirty. The solution is: 1 often cleaning, replace the filter core of the processor; 2 before booting the printing plate, thoroughly clean the developing machine, especially the rollers in the developing machine; 3 for floating on the plate, available Clean water first wipe off the protective rubber, use a small brush, dipped in a little developer liquid, and gently wipe it with clean water. Repeatedly, it can be removed (note that the dwell time on the plate must be short, otherwise it will Injury the small outlets around, and then wipe the protective gel.
4. Insufficient processing of plate development
When the developer (Kodak Premium CTP Positive Developer) is fatigued, for the Kodak Polyurray Graphics 0770×1030 plate, the layout of the blank part will be blue and the upper machine belt will be dirty. For this type of media, secondary development can be carried out to meet the printing quality requirements (but should pay attention to the development conditions, we usually adjust the development time, brush speed to twice the original, and must detect changes in the printing plate Internet point ).
In order to maximize the use of developer, while ensuring the quality of the printing plate, according to the fatigue of the developer, we can make up for the following two methods: 1 adjust the plate calibration curve value; 2 increase the development time or the development temperature or Increase brush speed.
All of the above methods can effectively reduce the scrapping rate in CTP plate making, thus reducing the cost of CTP plate making.
Source: Comin Media
Liquor is 90% marketing and what better way to grab attention than by having one of the coolest liquor bottles on the shelf? We should agree that taste is not the initial selling point for most consumers. That`s where marketing comes into play, and the bottle is a big part of that. An interesting look will get people to buy a brand at least once, and then it`s just a question of if the liquor inside is worth getting again. We would like to devote our passion on the Liquor`s dressing up.
Description
Usage
Liquor/Wine/Beverage
Material
Extra-flint, high-flint and flint glass
Technology
Machine made
Volume
50 to 3000ml or as your requirements
Weight
150 to 2000g and so on
Sealing type
Screw cap or cork
Painting
Any color as you requirement
Quality control
SGS, FDA, ISO9001, ISO14001
Deep processing
Silk screen, decal, spray painting,
electroplating, frosting, sand blasting.
Delivery term
EXW, FOB, CIF
Payment terms
T/T
Lead time
New design drawing confirm within 3days, Sample
mold within 20 days, bulk molds within 30 days, produce in bulk within 30 days
FAQ:
Q: Are you a manufacture or a trading company?
A: We are a manufacture which located in Chengdu city and Yibin city, Sichuan, China.
Q: Can you customize the products?
A: Yes, we are professional to customize glass bottle, we can design the new drawings and open the new molds according to your requirement.
Q: Do you provide free sample?
A: Yes, for cooperation sincerity, we are glad to provide you samples for free, but for new customer, the express cost need to be paid.
Q: What is your MOQ?
A: Our only standard for MOQ is a 40 feet container.
Q: How long is your sample lead time, mold need time and production lead time?
A: New design drawing confirm within 3 days, sample mold within 20 days, bulk molds within 30 days, produce in bulk within 30 days
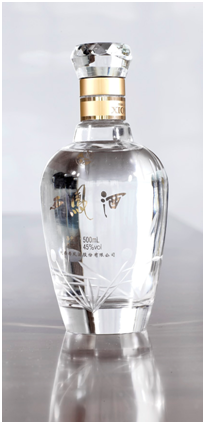
Wine Bottle
Wine Bottle,Round Wine Bottle,Decal Vodka Bottle,Red Character Wine Bottle
SICHUAN YIBIN GLOBAL GROUP CO.,LTD. , http://www.globalglassbottle.com