Wan Shizhe Ningxia Wuzhong City Reiter Paper Company, 751100
Dry-process papermaking uses air-settling technology and dry processing methods to make the fluff pulp strongly glued or melted using hot-melting fibers and fluff pulp. In the production process, no waste water or waste gas will be generated, which is easy to handle and meets the requirements of environmental protection. In the process of use, no fines can be produced, dry or wet, so its tensile strength and wet strength are particularly important. The factors affecting various physical indicators of dry paper in the production process are analyzed as follows:
First, glued clean paper (fluff pulp + latex)
The main process flow for glueless dustless paper production is:
(electrostatic treatment)
Pulp board → fiber separator → forming box → hot pressing → hot embossing → upper spray → oven #1 → under spray → oven #2 → curing box (puffing box) → finishing → calendering → coiling → Cutting → packing → storage
1. The effect of fluff pulp
Dustless paper is best made from pinewood sulfite fluff pulp with 100% natural plant fiber. The sulfite pulp has a higher degree of fiber polymerization than the kraft pulp, its fiber interior is flat, and the kraft pulp fiber interior is open. Choosing fluff pulp mainly considers whether to treat (softener treated) the average length of the pulp, fibers, dry elasticity (expressed in terms of the height of the dried fluff pulp sample at a pressure of 1.3 kPa), the fluid stagnation rate, and energy needed for the comminution. , moisture, whiteness, and fine fiber content. The clean paper produced from pulp processing is soft and comfortable, and the paper surface is smooth; the untreated pulp is rough and upright, but it has good liquid absorption and air permeability; the main indicator of the strength of the paper sheet is the average length of the fibers, and the longer the fiber, the more strength. Good, high degree of fibrosis, strength is better, generally choose the best between the length of 2.0 ~ 3.0mm; moisture above 7%, whiteness (ISO)> 80%; full processing pulp in the production process by the softener Treatment, high fluffiness, easy fiber separation, low separation energy, production of dust-free paper appears fluffy, that is, increased thickness, feel is also particularly good. The electrostatic treatment of the pulp sheet is also particularly important. Adding 1% antistatic agent to the pulp sheet can ensure that there will not be many slurries due to fiber separation and formation during the dry forming process, which will affect the quality of the product.
2. Shaped effects
The separated fluff pulp is dispelled into single fiber air and fed into a forming box screen cylinder. The nail roller equipped with densely-stirred nails further separates the fiber mass into single fibers, and is uniformly deposited by the screen under the action of airflow. On the moving forming web. Adjust the product quantification by adjusting the air flow and vacuum through the inlet fan and vacuum suction fan. When the web is formed, the strength is low and the density is small. The paper sheet is initially shaped by hot pressing. The dust-free paper produced with the high-mesh wire forming net has good density, smooth paper sheets, large liquid-absorbing capacity, high retention of fine fibers, and reduced flow fees. When the fiber is settled, special attention should be paid to the fact that the fibers should be arranged longitudinally more (ie, the running direction of the mesh), with less horizontal alignment, avoiding vertical alignment, and the strength of the dry paper and the page can be guaranteed. Production should be based on different quantitative products, adjust the forming negative pressure (ie, the pressure difference between the inlet and the vacuum pumping), in order to facilitate the formation of paper sheet to reduce the loss of small fibers and dust in the workshop, which is the key to air deposition technology.
Adjust the air volume and wind speed in the middle of the forming box to prevent the occurrence of air vortex, so as to avoid even sedimentation of the shadow fluff pulp. In order to fully break down the fluff pulp, the direction of the screen cylinder is designed to be opposite to the direction of the nail roller. It is especially important to prevent static electricity during the forming process. The forming net is an antistatic material. The inner surface of the forming box must also be an antistatic material. The surface should be smooth and flat, and there must be no protrusions or grooves to prevent hanging pulp and affect the appearance of the paper.
3. Effect of hot pressing
The formed paper web first enters into a compaction roll at about 140° C. to preheat pressure, so that the fiber layer is tight, and at the same time a certain number of fiber intertwining points are generated, the paper sheet has initial tightness, and then is introduced into the embossing area by the transfer network, and then enters. The high hot-pressing zone around 180°C is once again subjected to high-temperature and high-pressure treatment. The fibers are tighter and the number of fiber nodes increases. The webs that transmit the web can be adjusted and selected according to the needs, pressing out various kinds of flowers. The purpose of hot-pressing the dry paper sheet is to adjust the tightness and quantification of the paper sheet; the second is to press out various patterns such as plain weave, twill weave, and diamond-shaped net weave. With the same basis weight, plain weave paper has higher strength than other webs, and it has better softness and feel.
4. Adhesive (latex) and impact of glue system
The use of water-soluble latex in the production of clean paper should be based on the requirements of the production process. We currently use the German EN429, Japan UL-101, UL-102, Taiwan's KT-711, domestic VAE-05 series of dust-free paper Latex, its main components are ethylene-vinyl acetate, ethylene-acetate copolymer, propylene styrene copolymer (ACR) and SBR. Among them, EN429 latex is the best, its latex particle size is 0.2 micron, the minimum film-forming temperature is 0° C., the pH value is about 4, the lateral connection temperature is higher than 130° C., the maturation temperature is about 180° C., and the latex is wetted Strength agents, penetrants and other additives, make the paper sheet dry strength, but also have high wet strength, latex is a hydrophilic material, otherwise the paper will not absorb water. In order to make the paper produced without sourness, the degree of polymerization of the latex meets the requirements and free acid cannot exist. Latex can not be denatured, aged and agglomerated, the glass transition temperature, the minimum film-forming temperature, and the high-elastic state (a mechanical state in which a polymer with an amorphous linear shape and a slightly adhesive structure is within a certain range, also known as rubber (state) must meet the requirements.
The glue spraying system uses a porous spray nozzle to atomize the water-soluble latex onto the paper web with air. The amount of glue to be sprayed depends on the type of product. The spray nozzle generally selects an annular fan shape, the annular spray nozzle is atomized well, and the fan-shaped spray nozzle has a relatively strong penetration capability. Just below the glue dispensing system is a vacuum suction box that sucks in air to allow the glue to penetrate or penetrate the core of the sheet, preventing delamination and ensuring the strength of the sheet. The latex concentration should not be too large, the mesh should be clean, and the vacuum suction effect should be better. Otherwise, the latex will form a film on the surface of the sheet quickly, resulting in layering of the sheet and affecting the strength.
5. Drying effect
The sprayed wet paper sheet is dried in an oven at about 180°C. The first purpose is to use a hot air to make the adhesive chemically interact and cross-link with strength; secondly, the latex particles and the fibers are bonded to each other. Many knots are produced. This process is the key to the dry and wet strength of dustless paper. The dried paper sheet will also enter the puff box, making the paper sheet fluffy and soft. The temperature of the oven should not be too high, otherwise the latex will be aged, losing adhesion and elasticity. It is necessary to adjust the relationship between supply air and exhaust air so that the hot air penetrates the web to ensure the final strength of the paper sheet and to improve the softness and other physical properties of the paper sheet.
Second, heat sealing paper (hot melt fiber + fluff pulp)
The production process of heat-bonded and non-dusting paper only needs to add hot-melt fibers in the conveying process after the fluff pulp is crushed into fibers, and the rest is the same as glued and dust-free paper. The application of heat-bonded and dust-free paper is more extensive, and the liquid-absorbing property, padding property, softness and fluffiness are all superior to glued and dust-free paper.
1. Effect of hot melt fibers
The hot-melt fibers used are generally polyethylene and polypropylene (PE/PP: 1) skin core structure, and its skin melting point temperature is 135°C. There is a certain temperature difference between the skin layer and the core layer of the heat-melting fiber, and only the skin layer melts during production. The requirements for hot-melt fibers are mainly fiber length (4 to 10 mm), tensile strength, electrostatic treatment, curl, moisture regain, and oil content.
2. Effect of hot pressing
The formed paper sheet is a mixture of cellulosic fibers and hot-melt fibers of the fluff pulp. After hot pressing by the heat roller, cross-linking of the two fibers is performed by preliminary melting, and the heat-melting fibers PE/PP are evenly melted in the fibers to make the paper sheets. Closer. The temperature of the hot roller must not be too high, otherwise sticking may occur or the core of the hot melt fiber may melt.
3. Drying effect
After the hot-pressed web enters the hot-air drying oven, the heat-melting fibers are heated to the melting temperature of the bicomponent fiber cladding layer at a temperature of 135 to 150°C, and the surface produced by the heating itself is melted and flows to form fibers with the fibers. The thermal bonding point, when the strength has reached the requirements. However, it should be noted that the strength of the heat sealing paper mainly depends on the amount of hot melt fibers added and the appropriate temperature.
The dried sheet is treated with a foam-like surface treatment agent to prevent hair loss and then calendering.
Kraft Paper Bag without window supplier Richest Pack, wholesale high quality Kraft Paper Bags, food Kraft paper bag, Kraft paper valve bag for beef jerky, dried figs, shelled shrimp, coffee, coffee beans with competitive price and best service.
This type bags people can not see products from outside, but bags is more straight, more beautiful.
Detailed Production Description:
Material usually divided into three types:
2) Three layer materials composite;
3) Four layer materials composite;
Thickness: 50 ~ 250 microns by customized
MOQ: 10,000 PCS
Samples: Free Samples
Logo: Accept Custom Logo
Feature:Moisture proof
Sealing &Handle:Zipper top
Place of Origin: Shenzhen, China
Surface Handling: Gravure Printing
Color: up to 9 colors or customer requirement
Usage: healthy food, salted food, instant soup, etc.
Payment Term: EXW, FOB, CIF
Delivery Time: 12 ~ 15 work days
Packaging: Bundles/Cartons
Port of Loading: Shenzhen or Hong Kong

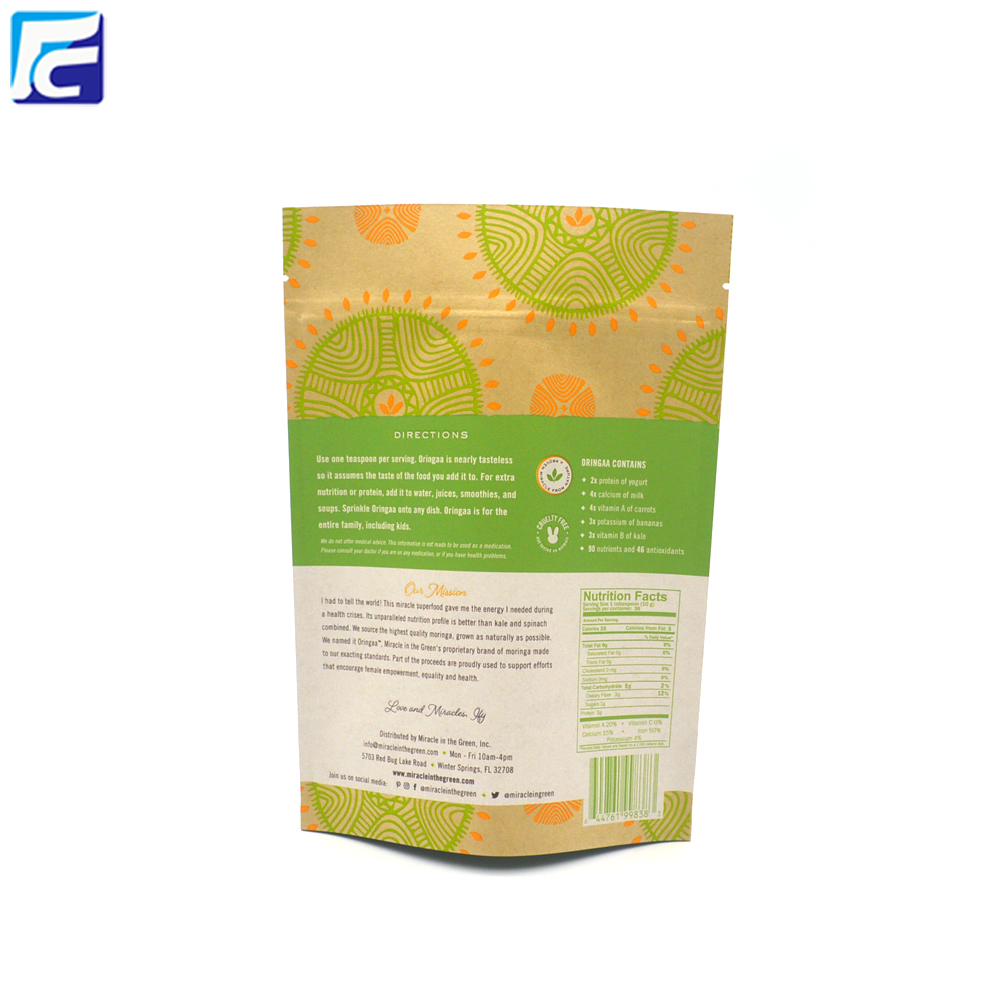
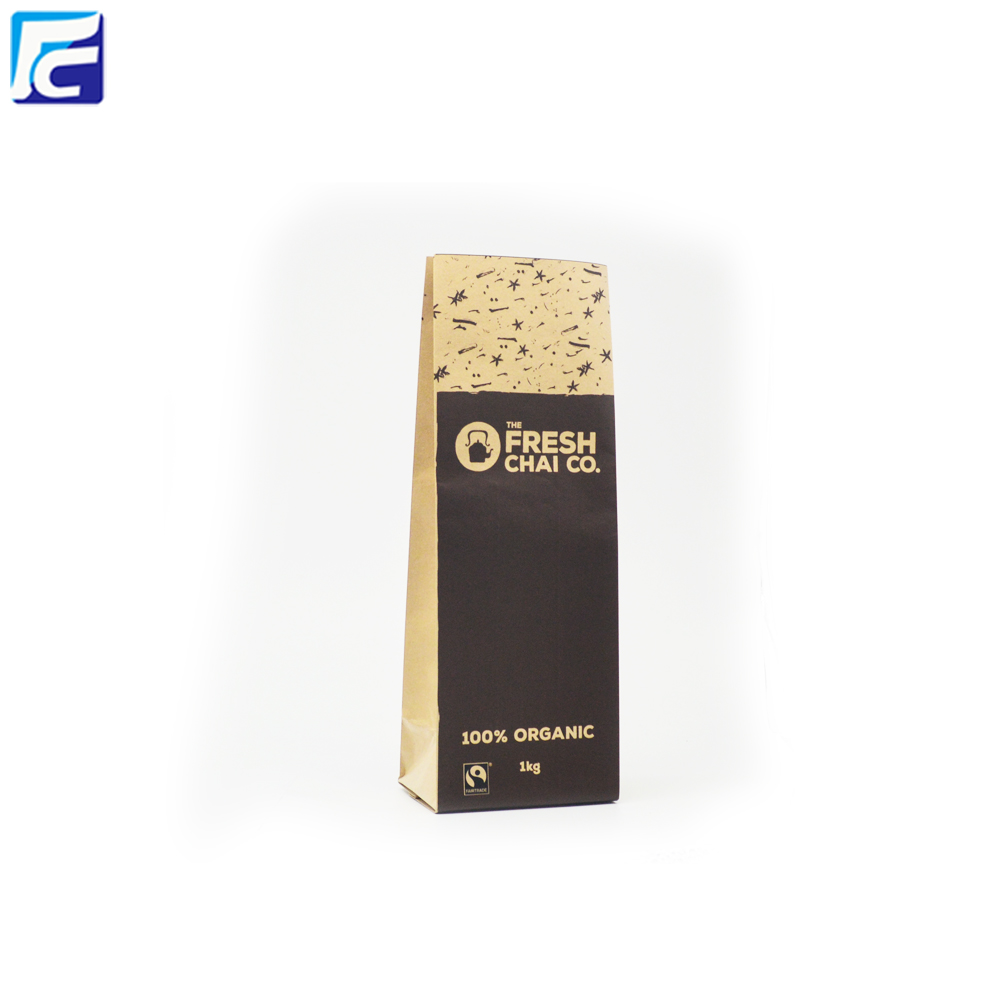
Kraft Paper Bags without Window
Kraft Paper Bags Without Window, Kraft Paper Bags, Snack Packaging Bags, Kraft Coffee Bean Bag
Richest Pack Limited , http://www.richestpack.com